It is thought that the first extraction of Alabaster in the Kirkby Thore area took place around 1790 when surface exposures were worked near Acorn Bank, a house dating back to the 13th century. No details exist of this working.
By 1829 workings for Alabaster were recorded at Potts Quarry and the material extracted was mostly used locally for the manufacture of “donkey” or “rubbing” stones used to whiten the edges of steps. The Alabaster was broken into cobbles, roasted for 24 hours, cooled for 24 hours, broken down further and then ground to a powder. The powder was then moistened and put into moulds to produce the stones which were about the size of a soap bar. By 1875 there were several producers and output was around 12,000 stones per week.
Commercial quarrying for Gypsum probably began in the 1850’s in small quarries near Stamphill Farm but it was not until the 1880’s that larger scale operations began.
The Boazman family, owners of Acorn Bank, opened the South Quarry near their house in 1880 and a few years later a second quarry (the North Quarry) was opened nearby to meet the demand for Gypsum. At this time, Gypsum was used in the glass manufacturing process for polishing purposes and material was sent to Pilkingtons at St. Helens and the Union Plate Glass Co. at Newcastle. Material for St. Helens was dispatched from Newbiggin Station and that for Newcastle went via the North Eastern Railway from Temple Sowerby Station.
In 1888 Joseph Robinson & Co. who had been extracting Gypsum in the Cotehill area since the 1820’s, acquired land near Stamphill and developed two quarries which were known as Robinson’s Quarry and Hunter’s Quarry. The material produced was transported to Long Marton Station for onward distribution.
By 1890 the quarries at Acorn Bank were becoming difficult to work and the decision was taken to drive an exploratory adit into the North Quarry face and continue working by mining. Operations at Acorn Bank were on a small scale with probably only 4 or 5 miners employed.
Further quarrying began in 1905 when the McGhie brothers from Kirkby Thore leased land adjacent to the S&C railway near Bridge 263 and developed Malley Hill Quarry. It took over a year to expose the Gypsum and production began in 1906 when agreement was reached with the Midland Railway for the construction of a siding (McGhies’ siding). Initially Gypsum was sent to McGhies’ own processing plant at Rutherglen near Glasgow, but by 1912 a mill had been built close to their quarry.
It soon became apparent that dealing with the overburden at the quarry was restricting potential expansion and in 1907 exploration underground began. By 1914 business was increasing and McGhies had developed their “Thistle Brand” of hardwall plaster which was very successful.
In 1911 Robinson & Co. amalgamated with Howe & Co. and the Long Meg Plaster Co. to form the Carlisle Plaster and Cement Company. Due to under-capitalisation, this company went into receivership and in 1918 was taken over by the Gotham Company of Nottingham.
Around this time, Gypsum produced from Robinson’s Quarry and Hunter’s Quarry was being transported by rail for processing at Cocklakes Mill near Cotehill.
At Acorn Bank in 1923 a second adit was driven into the Gypsum deposit and a wire rope installed to assist with the movement of tubs of mined material. The wire rope system was powered by a water wheel in the nearby corn mill which had existed for hundreds of years.
Demand for Gypsum continued to increase and by 1924 McGhies were unable to produce enough material from their own resources so negotiated a five-year agreement with the Boazmans at Acorn Bank to supply 12,000 tons per year for McGhies to process.
In 1925 the Gotham Company took over the Boazman mine and company and sought to improve the operation. In 1926 an aerial ropeway some 2 miles long was constructed to carry material from the Boazman mine to McGhies processing plant which considerably increased output. An engine house was constructed for the Crossley oil engine that powered the ropeway. Improvements were also made to underground ventilation which enabled the workings to expand.
Although reserves of Gypsum, proven by surveys in 1934, were still present, operations at the Boazman mine ceased and it was closed in 1937. Little remains to be seen of operations here except for the quarry (now flooded and very overgrown), the site of the later adit (now filled in), a former Gunpowder Store and the engine house adjacent to the road from Temple Sowerby to Newbiggin. Acorn Bank is now a National Trust property open to visitors in the summer months and within the grounds, the edge of the quarry and the buildings are accessible.
Meanwhile, the Gotham Company, already owning the Robinson and Hunter Quarries had taken over the McGhie company in 1927 so was now the sole company operating in the Kirkby Thore area. Following this take over, a new drift was driven in the area of the Robinson and Hunter Quarries and underground working commenced in what was called the Stamphill mine.
During the 1930’s demand for Gypsum products increased considerably and the underground workings were expanded by driving further drifts. Exploration by drilling boreholes was also carried out to identify further deposits. This identified two additional locations where mining was likely to be possible. One of these was the Birkshead Mine, which still operates today. These two sites were further away from the mill than previous mines and quarries so in addition to the aerial ropeway from the Boazman Mine, a system of overground conveyor belts and further aerial ropeways was installed to transport the excavated material to the mill.
To cope with demand, the mill itself was upgraded with a new plant being constructed by 1934 adjacent to McGhies’ mill. Expansion underground at this time meant that the workings from the McGhie mine now extended beneath the S&C railway. The railway company was obliged by Legislation, dating from 1923, to pay compensation to the mine operators for them to extract the minimum amount of material from beneath the railway to limit subsidence.
In 1935 the Gotham Company amalgamated with British Plaster Board and the new concern was faced with a significant rise in the demand for Gypsum as the type of house now being built was semi-detached, larger than the earlier terraced houses, requiring more cement and plaster. The Hunter, Robinson and McGhie Quarries were almost worked out as was the Stamphill mine, opened in 1927 and the McGhie mine.
Production at the new Birkshead Mine began and in 1937 a new mine was opened at Stamphill.
The McGhie mine was closed in October 1939.
Work continued during the war and in the late 1940’s work began to drive a connection underground between the two mines to exploit further reserves.
The post-war increase in building work gave rise to a massive demand for Gypsum and in the late 1950’s it was decide to construct a new plant capable of increasing production capacity by 60,000 tons per year along with a new plaster board mill which would produce 15 million square metres of board per year (see British Gypsum Plaster Works, Kirkby Thore).
A new quarry was opened at Houtsay near Acorn Bank in 1960 which proved to be very successful. As excavation became deeper an entrance was created in the eastern quarry face and a new mine known as Newbiggin Mine opened in 1961. This was a small mine which in time produced much lower quantities than either Longriggs or Birkshead. Unfortunately, in the late 1960’s there was a serious roof fall in this mine resulting in two fatalities. This mine closed in 2005.
Increased mechanisation of the extraction process took place with continued expansion underground and in 1965 another new mine was opened at Longriggs, to the south of the Kirkby Thore plant.
Birkshead Mine was the largest of the mines and required updating to accommodate the latest methods of mining. A new drift was driven for access and crushing plant was relocated underground. A new conveyor system was also installed to carry the crushed material from the mine to storage bins underground in Longriggs Mine and then onwards to the mill.
This system of conveyor belts enabled the various aerial ropeways to be dismantled and work began on this in 1975. The conveyor belts are still in use today and with their green corrugated cover are a prominent feature in the local landscape. A conveyor passes beneath the S&C in a dedicated underbridge (Bridge 260C) at 281 miles, 18 chains.
The Stamphill mine suffered a collapse in 1972 resulting in settlement of around 15 feet in the overlying ground covering an estimated 13 acres. Fortunately, it occurred on a Sunday and no one was underground at the time. Following the collapse, the size of the pillars left in place after mining was increased. Stamphill was virtually worked out and production was concentrated on Newbiggin, Birkshead and Longriggs Mines.
By the mid 1970’s production from the three mines was 750,000 tons per year which translated to 4,000 tons of bagged plaster and 750,000 square yards of plaster board per week.
In the 1980’s environmental concerns saw the introduction of measures to reduce the emissions, particularly sulfur dioxide, from coal fired power stations by 2000. The processes developed to achieve this passed the flue gases through limestone slurry filters. Once used, the slurry could be chemically treated to convert the limestone to gypsum which could then be offered as a by-product. This became available around 1994 and was a plentiful source also being a cheaper alternative to mined Gypsum. The largest source of what was known as Desulfogypsum was Drax power station in North Yorkshire and this supplied upwards of 250 tons per day by rail to Kirkby Thore. The imported material was blended with Gypsum from Birkshead Mine at a ratio of 30% Birkshead to 70% Drax. Material was also imported from Fidlers Ferry power station near Warrington. This new source of supply caused a reduction in the number of mining staff employed at Kirkby Thore. However, the declining use of coal fired power stations inevitably led to a reduction in the availability of Desulfogypsum and, as of November 2022, this source of gypsum was no longer being used at Kirkby Thore. Instead, the local supply of mined gypsum was being supplemented by imported gypsum. The latter is delivered to the site by rail via an average of four trains per week, with each train consisting of a loco plus seven container carrier wagons (with each wagon carrying three 20-foot open-topped containers). Each container is theoretically capable of carrying approximately 36 cubic metres of material, which equates to around 70 to 75 tonnes. The full trains usually arrive from the south in the early hours of the morning, with the 'empties' returning south later the same day. The containers are unloaded by a mobile grab and dump trucks transfer the gypsum to a storage area within the plant.
Both the mining and manufacture of Gypsum based products continues at Kirkby Thore today although only the Birkshead Mine remains in use. All the previous quarry and mine locations have now been cleared and landscaped so there is little evidence, beyond the production plant and conveyor belts, of the scale of operations that has taken place in this area. Even the above ground infrastructure at Birkshead has been reduced to the point where it is not obvious what the purpose is of the building visible from the local roads.
Image Gallery
Image 1
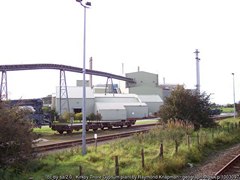
Photo © Raymond Knapman
(cc-by-sa/2.0), source:
https://www.geograph.org.uk/photo/1003097.
Image 2
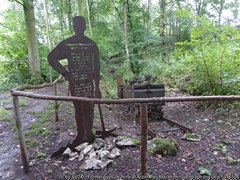
Photo © Marathon
(cc-by-sa/2.0), source:
https://www.geograph.org.uk/photo/5916506.
Image 3
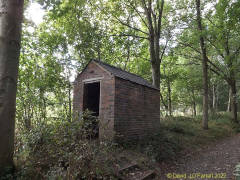
Image 4
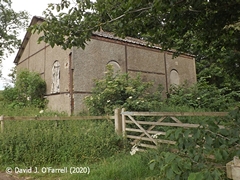
Image 5
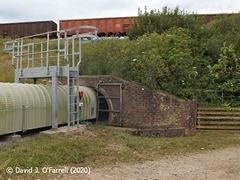
Image 6
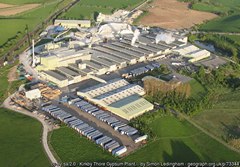
Photo © Simon Ledingham
(cc-by-sa/2.0), source:
https://www.geograph.org.uk/photo/73344.
The relationship with the Settle-Carlisle Railway
The railway played a large part in the development of the Gypsum industry at Kirkby Thore and four different facilities were provided between Long Marton Station and Newbiggin Station by the Midland Railway and its successors. These are all illustrated in “Stations & Structures of the Settle & Carlisle Railway” [1].
From 1888, Joseph Robinson & Co had transported material from their quarries to the sidings at Long Marton Station for onward distribution and then, in 1924, the LMS entered into an agreement with the Gotham Company (who had taken over Joseph Robinson & Co) for the provision of sidings at milepost 281¾ to tranship Gypsum from the internal quarry tramways. A lever frame was provided, protected by fixed signals.
Further north, near milepost 282, in 1906 the Midland Railway constructed a siding to serve Thomas McGhie’s Thistle Plaster Works. This was controlled by a 4 lever ground frame until 1947 when control transferred to Long Marton Signal Box. In 1970 Long Marton Signal Box was closed and control passed to Appleby North Signal Box until 1994 when British Rail erected two Portacabins to create Kirkby Thore Signal Box which is still in use. These sidings have been extended as the works have developed and are still in use today (see SCRCA site 281981: British Gypsum Plaster Works, Kirkby Thore).
The sidings at Newbiggin Station near milepost 283½ were also used for Gypsum traffic, with a dedicated loading dock adjacent to Bridge 271. This facility was initially provided for Boazmans at Acorn Bank but when they were taken over by the Gotham Company, Gotham entered into an agreement with the LMS in 1926 to buy the facility off the railway and maintain it.
The Boazman mine was closed in 1937 and use of the facility ceased. With the opening of the Newbiggin Quarry and Mine in the 1960’s, the siding at Newbiggin was reinstated and extended in 1968 for the storage and despatch of material.
Railway Locomotives
A number of locomotives have been operated in conjunction with the quarrying and mining operations at Kirkby Thore.
In 1890 Robinsons acquired an 0-4-0 ST built by John Fowler and an 0-4-0 ST built by W G Bagnall both of which were thought to be 24” gauge to transport material from the quarry to the plant. A further Bagnall 0-4-0 ST, no. 2060, 36” gauge, arrived in 1917. Both of the 1890 locos worked until the 1920’s and are thought to have been disposed of by burying in a disused area of the quarries.
In 1942 the Andrew Barclay 0-4-0 ST “WTT” (Works no. 2134) was acquired for use in McGhies’ sidings. At some stage in its life, it has carried the name “Coronation”. This loco was bought for preservation and moved to Carnforth in 1970 with three other Andrew Barclay locos from British Gypsum. It is not known where this loco is currently.
In 1947 a second-hand locomotive was purchased from the Barrow Haematite Steel Company to shunt in McGhies’ sidings. This was a W G Bagnall 0-4-0 ST (Works no. 1494) dating from 1896.
Since all the Gypsum production at Kirkby Thore, Cocklakes and Long Meg was carried out by the same company, there was some transferring of standard gauge locos between the sites as required. Thus in 1952 the Andrew Barclay 0-4-0 ST “J N Derbyshire” was transferred from Cocklakes to Kirkby Thore.
1953 saw the acquisition of the final steam locomotive for Gypsum operations. This was another Andrew Barclay 0-4-0 ST (Works no. 2343) numbered 4 (British Gypsum no. 4). In 1965 it was renamed “Ken Boazman” after one of the company Directors and was one of the four locos that went to Carnforth in 1970. Today it is at the Ribble Steam Railway awaiting repairs (https://ribblesteam.org.uk/).
1968 saw the arrival of an Andrew Barclay 0-4-0 Diesel Hydraulic loco (Works no. 552) named "FGF" after F. G. Flood, one of the company Directors. In 2011 this loco motive was donated by British Gypsum to the Scottish Railway Preservation Society and is now located at the Bo’ness and Kinneil railway. https://www.bkrailway.co.uk/
Two further Andrew Barclay Diesel Hydraulic loco (Works nos. 558 and 559) named "JWH" (J. W. Hunter) and "BG" (British Gypsum) arrived in 1970. These diesels worked at Kirkby Thore, Cocklakes and Long Meg and their arrival saw the disposal of four of the 0-4-0 saddle tanks as mentioned above. The whereabouts of these latter diesel locomotives is not known.
Further Reading
For a general introduction to the gypsum industry in the Eden Valley and its relationship with the S&C, see The Gypsum Industry and the Settle-Carlisle Railway. You may also find the following of interest: Gypsum Production in the Cotehill Area and Long Meg Mine, Little Salkeld.
[1] Details of the four gypsum facilities and their related sidings can also be found in “Stations & Structures of the Settle & Carlisle Railway” by V R Anderson & G K Fox (Oxford Publishing Company, 2nd edition 2014 ISBN 978 0 86093 662 6).
Acknowledgements
This article was researched and written by David O'Farrell specifically for the SCRCA web-portal. Illustrations and photographs by the author, except where otherwise stated.